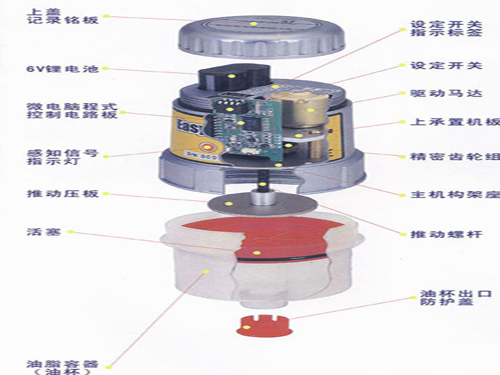
Nowadays, more and more companies are pursuing high production efficiency. With the development of automation equipment and technological advancement, the requirements of enterprises for mechanical equipment are also increasing, and the extended requirements for equipment stability and long-term operation of machinery Whether to keep up with the pace of business, this issue has also begun to pay attention to companies.
The development of a company is accompanied by the development of human resources. At the same time, simple and repetitive tasks are replaced by mechanical locks. If the machinery is damaged, then the productivity of the enterprise is bound to be affected, and how to avoid or reduce the damage rate of mechanical equipment. This can be further extended to the maintenance and maintenance of mechanical equipment. How to maintain mechanical equipment?
Our traditional method is to perform maintenance during the company's leisure time, or stop the equipment from working and add lubricating grease, so as to simply maintain the equipment.
Some machinery is the need for long-term operation of the machinery, or some dangerous areas, hard to reach the artificial area how to maintain it?
The equipment maintenance methods described above are also used to maintain the lubrication of the equipment. What is the solution to solve it? As a result, the devices for automatic lubrication and maintenance have also emerged one after another. So how do we select the appropriate or mechanically-specific automatic lubrication and maintenance device for machinery?
Automatic lubricators are the most well-known two or three brands on the market. Taiwan's Easylube Single Point Reusable Lubricator and U.S. Pulsarlube Single Point, Multipoint, Disposable, Repeatable Automatic Lubricator Plus Potentlube Multipoint Centralized lubrication pump (for details, contact your professional agent).
According to the actual situation of the equipment, it is equipped with a suitable lubrication device (including the amount of oil used for the device, the frequency of oil injection, the number of points the device needs to be lubricated, etc.)
It is also necessary to consider the use of mechanical equipment in some hazardous areas (eg special greasers for explosion-proof motors, special greasers for petroleum and mining machinery and equipment, and how to use the characteristics of some brands).
Recommendations for bearing maintenance using the Easylube oiler:
Bearing diameter 35-48mm 15 to 18 grams per month Grease bearing diameter 49-62mm 18 to 26 grams per month Grease bearing diameter 63-78mm 26 to 37 grams per month Grease bearing diameter 79-87mm 37 to 50 per month Grease
Oxide powder for thermal spray refers to a type of powder material that is used in thermal spray processes. Thermal spray is a coating technique where a material in powder form is heated and propelled onto a substrate, forming a coating.
Oxide powders are commonly used in thermal spray applications due to their high melting points, excellent wear resistance, and thermal insulation properties. They can be used to create protective coatings on various surfaces, such as metals, ceramics, and plastics.
Some common types of oxide powders used in thermal spray include:
1. Aluminum oxide (Al2O3): This oxide powder is widely used for its high hardness, wear resistance, and thermal insulation properties. It is commonly used for coating applications in industries such as aerospace, automotive, and electronics.
2. Zirconium oxide (ZrO2): Zirconium oxide powder is known for its high melting point and excellent thermal barrier properties. It is often used in thermal spray coatings for gas turbine engine components, where thermal insulation is critical.
3. Chromium oxide (Cr2O3): Chromium oxide powder is used for its high hardness, corrosion resistance, and wear resistance. It is commonly used in applications where high temperature and abrasive wear resistance are required.
4. Titanium oxide (TiO2): Titanium oxide powder is known for its high refractive index and excellent UV resistance. It is often used in thermal spray coatings for optical and decorative applications.
These oxide powders can be applied using various thermal spray techniques, such as flame spraying, plasma spraying, or high-velocity oxy-fuel (HVOF) spraying. The choice of oxide powder and thermal spray technique depends on the specific application requirements and desired coating properties.
Oxide Ceramics Powder,Pure Aluminum Oxide Powder,Chromium Oxide Ceramics Powder,Yttria Stabilized Zirconia Powder
Luoyang Golden Egret Geotools Co., Ltd , https://www.lygoldentool.com