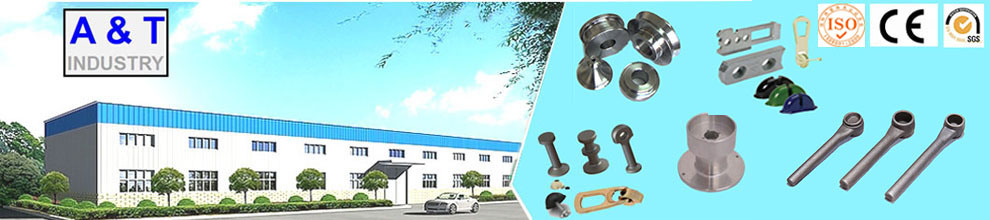
Quick Details
Place of Origin: |
Shandong China (Mainland) |
Brand Name: |
AT |
Model Number: |
A&T investment casting |
Application: |
Carbon Steel Pipe Fittings |
Material: |
Steel |
Dimensions: |
Water Glass Castings |
Casting: |
stainless steel |
Packaging & Delivery
Packaging Details: |
Standard Exporting Packaging |
Delivery Detail: | 30 Days |
Manufacturing Process of Nantong JianXiang Casting:
Investment Casting or Lost-wax Casting, focus on materials of Carbon Steel, Stainless Steel.
Sand Casting, Focus on materials of Iron, Steel and Aluminum.
Die Casting, Aluminum Alloy, Zinc Alloy.
CNC Machining,Turning,Milling,Drilling and Grinding on the castings
Â
Quality Certification:
We are ISO9001:2008 Certified, we offer below testing and report:
Spectral Analysis, Full Dimension Report, Material Certification, Mechanical Performance Testing, Hydro Testing, Ultrasonic inspection could be provided on our casting parts.
Â
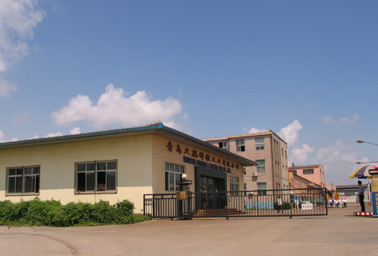
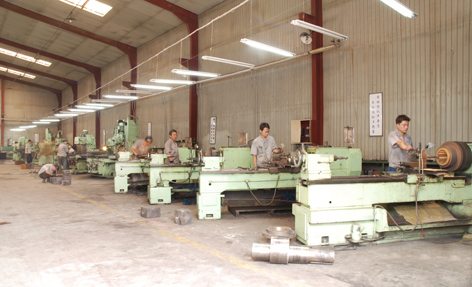
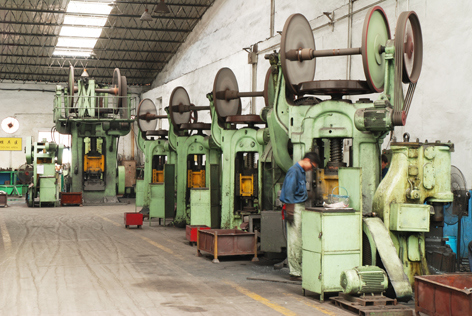
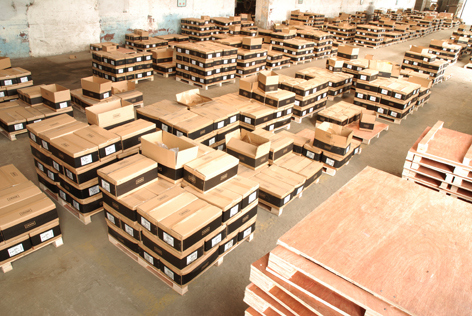
Â
Â
Our Main Products:
Stainless Steel Casting, Carbon Steel Casting, Alloy Steel Casting, Aluminum Casting, Bronze Casting, Iron Casting ,Impellers, Bearing Seat/Cap, Valve Body, Valve Housing, Pump Housing, Pump Case, Valve Balls, Turning Shaft, Manifold, End Covers, Washers, Pump Parts, Automobile castings, Stainless steel marine hardware casting parts, architecture hardware, Copper alloy castings, Mining & Earthmoving machinery accessories, Ships & Train & Automobile & Motorcycle fittings, Electric machine & hardware fittings etc.
Â
Â
What Surface Treatment can we offer:
Zinc plating/Galvanized, Chrome plating, Polishing, Painting, Powder coating, Shot blasting,
Sand blasting, Phosphating, Grinding, Electrophoresis, Anodizing, Black Oxide etc.
Â
Material Standard we can Follow and produce:
GB. ASTM. AISI. DIN. BS. JIS. NF. AS. AAR
Investment Casting: 201, 202, 303, 304, 304L, 316, 316L, 1Cr18Ni9Ti, 430, 440, 1008, 1020, 20NiCrMo, 30CrMo, 42CrMo4
Sand Casting: Ductile Iron, Gray Iron, Aluminum, Steel etc.
Die Casting: ADC12, A380, A356, ZAMAK 3, ZAMAK5 etc.
Â
Manufacturing Limitations:
Max linear Size:2200mm; Max Diameter Size:1000 mm
Casting Weight range: 0.02~2000Kg
Â
Best Casting Surface Roughness: Ra 3.2um~12.5um(by Investment Casting and Die Casting)
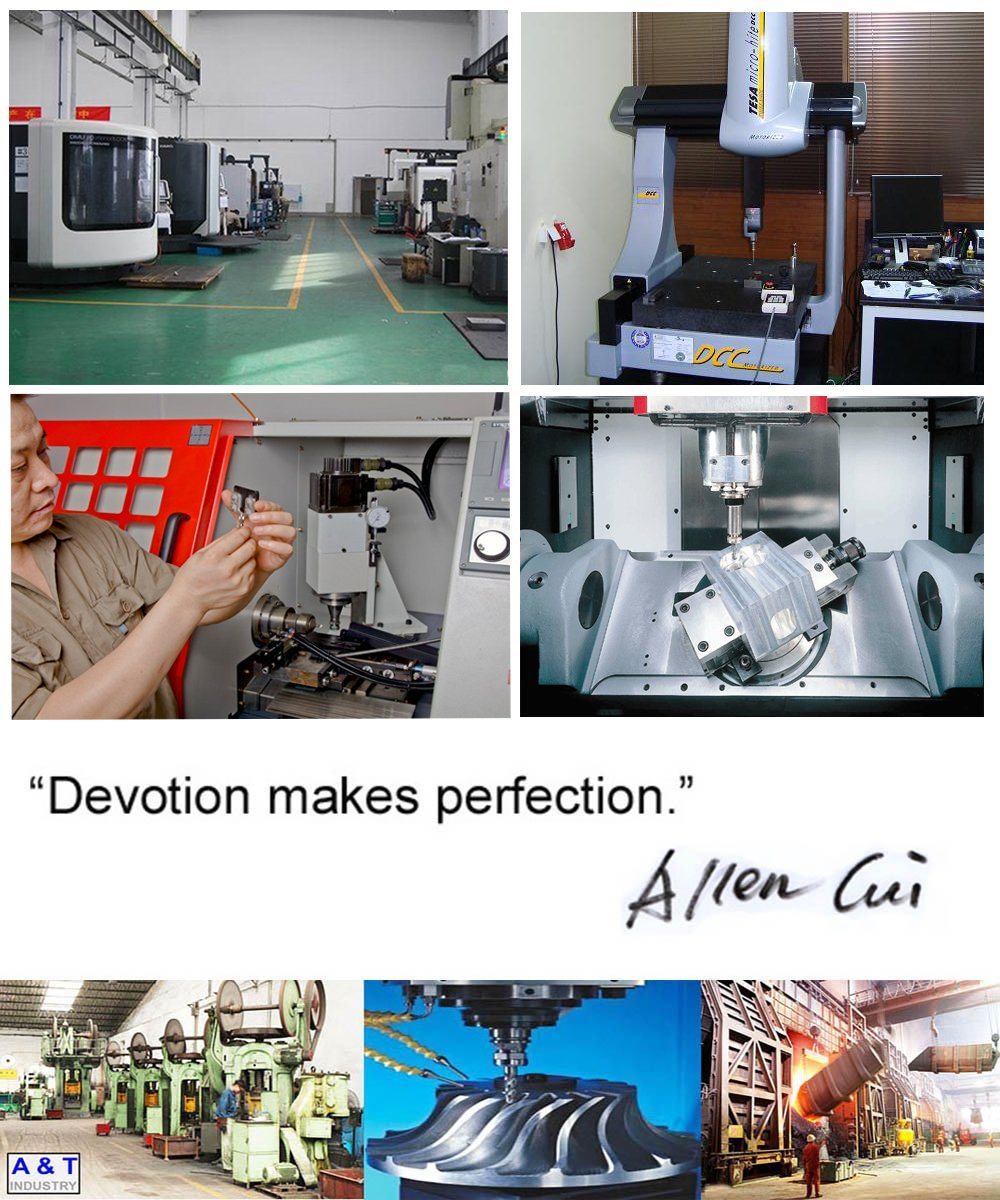
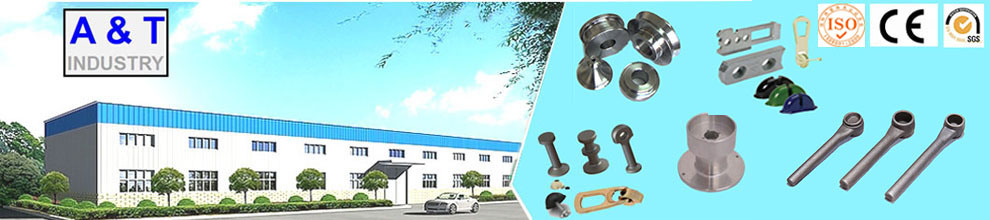
Quick Details
Place of Origin: |
Shandong China (Mainland) |
Brand Name: |
AT |
Model Number: |
A&T investment casting |
Application: |
Carbon Steel Pipe Fittings |
Material: |
Steel |
Dimensions: |
Water Glass Castings |
Casting: |
stainless steel |
Packaging & Delivery
Packaging Details: |
Standard Exporting Packaging |
Delivery Detail: | 30 Days |
Manufacturing Process of Nantong JianXiang Casting:
Investment Casting or Lost-wax Casting, focus on materials of Carbon Steel, Stainless Steel.
Sand Casting, Focus on materials of Iron, Steel and Aluminum.
Die Casting, Aluminum Alloy, Zinc Alloy.
CNC Machining,Turning,Milling,Drilling and Grinding on the castings
Â
Quality Certification:
We are ISO9001:2008 Certified, we offer below testing and report:
Spectral Analysis, Full Dimension Report, Material Certification, Mechanical Performance Testing, Hydro Testing, Ultrasonic inspection could be provided on our casting parts.
Â
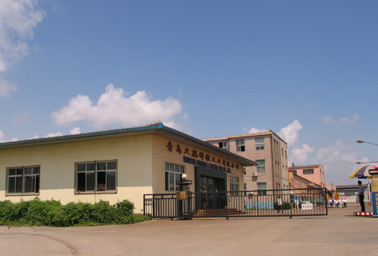
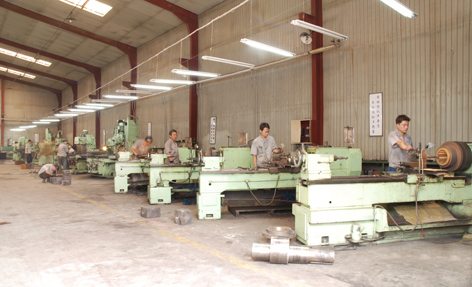
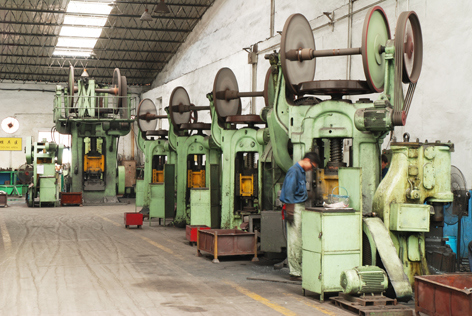
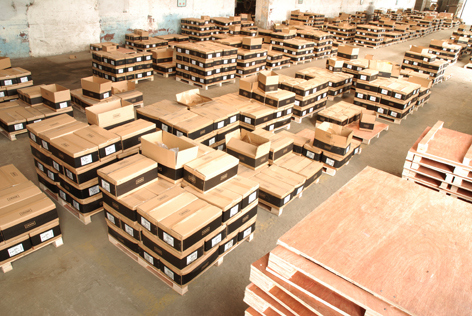
Â
Â
Our Main Products:
Stainless Steel Casting, Carbon Steel Casting, Alloy Steel Casting, Aluminum Casting, Bronze Casting, Iron Casting ,Impellers, Bearing Seat/Cap, Valve Body, Valve Housing, Pump Housing, Pump Case, Valve Balls, Turning Shaft, Manifold, End Covers, Washers, Pump Parts, Automobile castings, Stainless steel marine hardware casting parts, architecture hardware, Copper alloy castings, Mining & Earthmoving machinery accessories, Ships & Train & Automobile & Motorcycle fittings, Electric machine & hardware fittings etc.
Â
Â
What Surface Treatment can we offer:
Zinc plating/Galvanized, Chrome plating, Polishing, Painting, Powder coating, Shot blasting,
Sand blasting, Phosphating, Grinding, Electrophoresis, Anodizing, Black Oxide etc.
Â
Material Standard we can Follow and produce:
GB. ASTM. AISI. DIN. BS. JIS. NF. AS. AAR
Investment Casting: 201, 202, 303, 304, 304L, 316, 316L, 1Cr18Ni9Ti, 430, 440, 1008, 1020, 20NiCrMo, 30CrMo, 42CrMo4
Sand Casting: Ductile Iron, Gray Iron, Aluminum, Steel etc.
Die Casting: ADC12, A380, A356, ZAMAK 3, ZAMAK5 etc.
Â
Manufacturing Limitations:
Max linear Size:2200mm; Max Diameter Size:1000 mm
Casting Weight range: 0.02~2000Kg
Â
Best Casting Surface Roughness: Ra 3.2um~12.5um(by Investment Casting and Die Casting)
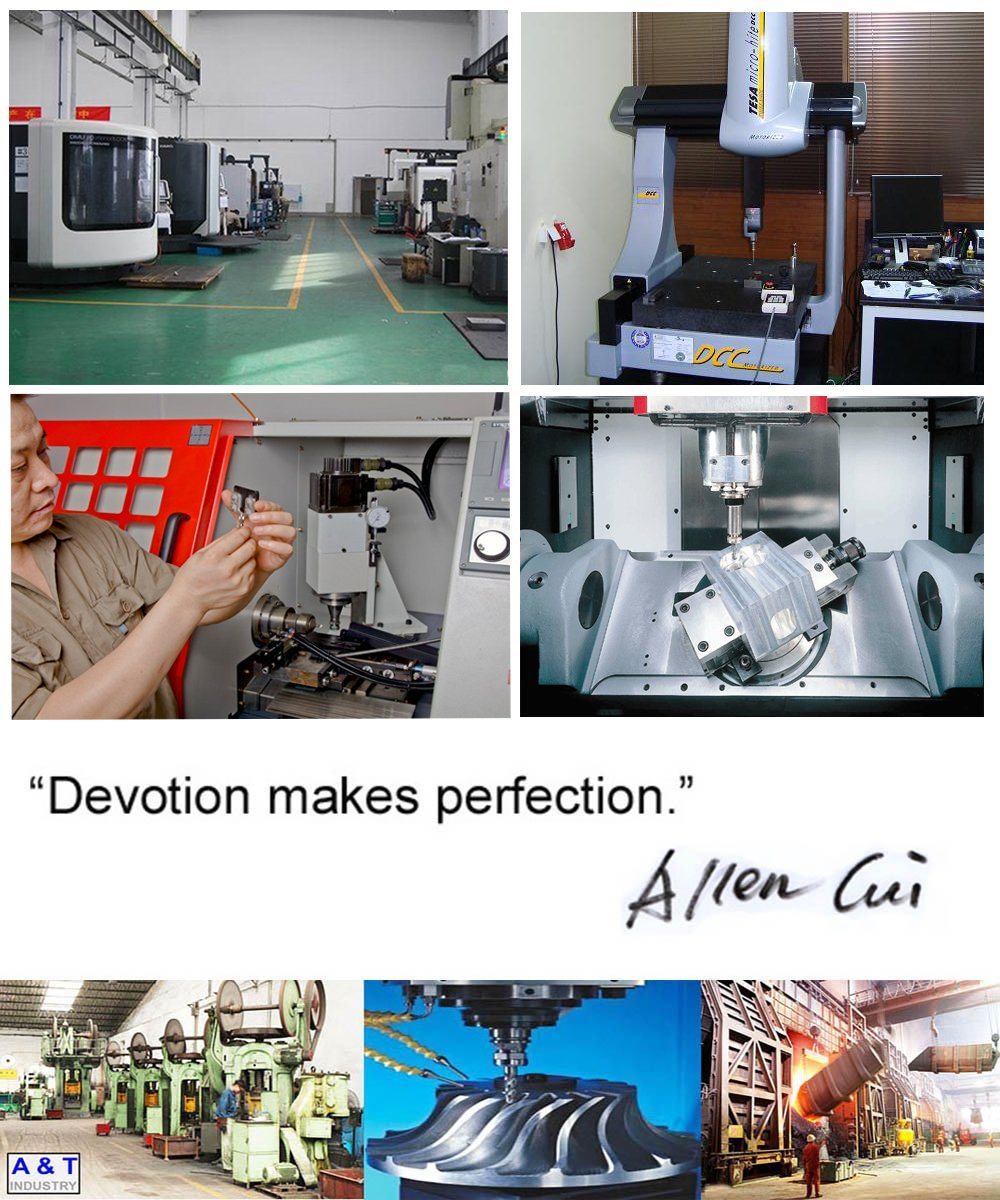
Cobalt-based alloy powders are commonly used in plasma transfer arc welding (PTAW) due to their excellent high-temperature properties and resistance to wear and corrosion. These alloys are typically composed of cobalt as the base metal, with various alloying elements such as chromium, tungsten, nickel, and carbon added to enhance specific properties.
The use of cobalt-based alloy powders in PTAW offers several advantages, including:
1. High-temperature strength: Cobalt-based alloys exhibit excellent strength and resistance to deformation at elevated temperatures, making them suitable for welding applications that involve high heat.
2. Wear resistance: These alloys have a high hardness and resistance to wear, making them ideal for welding applications where the welded parts are subjected to abrasive or erosive conditions.
3. Corrosion resistance: Cobalt-based alloys offer good resistance to corrosion, making them suitable for welding applications in aggressive environments, such as those involving chemicals or saltwater.
4. Thermal conductivity: Cobalt-based alloys have good thermal conductivity, allowing for efficient heat transfer during welding and reducing the risk of heat-affected zone (HAZ) defects.
5. Compatibility with other materials: Cobalt-based alloys can be easily welded to a wide range of base metals, including stainless steels, nickel alloys, and other cobalt-based alloys, providing versatility in welding applications.
To use cobalt-based alloy powders for PTAW, the powder is typically fed into the plasma arc using a powder feeder. The powder is then melted by the high-temperature plasma arc and deposited onto the workpiece, forming a weld bead. The specific welding parameters, such as arc current, travel speed, and powder feed rate, will depend on the specific alloy and application requirements.
It is important to note that the selection of the cobalt-based alloy powder should be based on the specific welding application and the desired properties of the final weld. Different cobalt-based a
Co Powder,Cobalt 6 Powder,Cobalt 12 Powder,Cobalt 21 Powder
Luoyang Golden Egret Geotools Co., Ltd , https://www.xtchvof.com