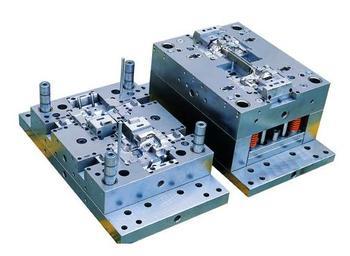
Mold design depends on the type of molding equipment. Therefore, it is necessary to know the performance, specifications, and characteristics of various molding equipment. For example, for the injection molding machine, the following contents should be understood in terms of specifications: injection capacity, clamping pressure, injection pressure, mold installation size, ejection device and size, nozzle hole diameter, and nozzle radius, size of the gating sleeve, Maximum thickness and minimum thickness of die, template stroke, etc.
The increasing size of die-molded parts and the high productivity of parts require a multi-cavity mold, resulting in an increasingly larger die, large-tonnage large-scale die up to 100 tons, a mold of several hundred lumens, thousands of chambers, requiring large-scale mold processing equipment Taiwan, increased y-axis z-axis travel, high load-bearing rigidity, and high consistency. The hardness of the mold steel material processed by the mold is high, and the mold processing equipment is required to have thermal stability and high reliability.
For complicated cavity and multi-functional compound molds, with the complexity of the shape of the parts, the level of design and manufacture of the mold must be improved, and a variety of grooves and various materials must be formed or assembled into a multi-functional composite assembly in one set of molds. The mold requires a large amount of processing and programming procedures. It has a high deep hole cavity comprehensive cutting capacity and high stability, and improves the processing difficulty.
The refinement of mold processing brings more attention to the compoundness and high efficiency of processing equipment. High-speed milling has many advantages such as high machinability, stable machining, small cutting force, and small workpiece temperature deformation, which makes mold companies pay more and more attention to high-speed machining.
The static performance introduced by the machine tool manufacturer cannot reflect the actual machining situation when machining the three-dimensional mold surface. The high-precision machining of the three-dimensional surface of the mold also puts forward the requirements of high dynamic precision performance. The high-speed high-precision can only be realized by the combination of high rigidity, heat-defining, high reliability, and high-quality control systems of the machine tool.
auto fuse types, cartridge fuse for car, automotive blade fuse, atc blade fuse, littelfuse mega fuse
Taishan Yuanjin Auto Parts CO., LTD , https://www.yuanjinautoparts.com